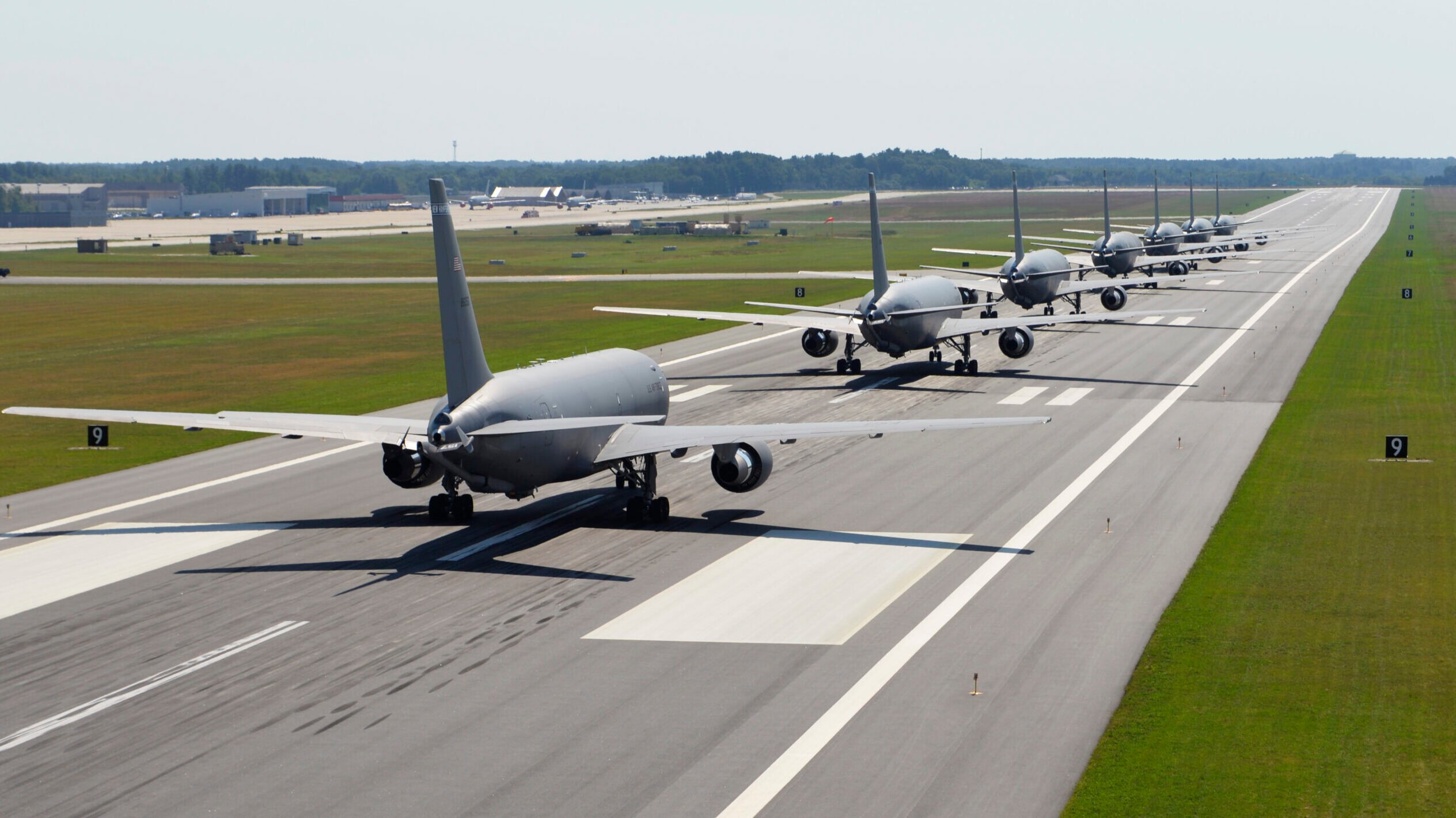
KC-46A aircraft assigned to the 157th Air Refueling Wing perform an elephant walk formation on the runway at Pease Air National Guard Base, Sept. 8, 2021. (U.S. Air National Guard Photo by Senior Master Sgt. Timm Huffman)
UPDATED 1/19/24 at 11:48 AM ET: This story was updated with new information provided by the Air Force on the status of category 1 deficiencies.
EVERETT, Wash. — In the wake of Boeing’s KC-46A Pegasus topping $7 billion in losses, company officials have been eager to stem the tide of the tanker’s long-running woes — and resolve several critical issues that pose risks to its operations.
The Pegasus currently has six category 1 deficiencies, Air Force terminology for problems that could cause loss of an aircraft, injury, or death. Spending money to fix those issues has helped drive Boeing’s staggering losses on the program, and is a key reason why company officials have sworn off fixed-price development contracts like those that govern the KC-46A.
Work to address the tanker’s predicaments starts in the Seattle suburb of Everett, Wash., where Boeing builds the commercial 767 and converts it into the KC-46A tanker. In a recent tour of these facilities, Breaking Defense spoke with company officials about how they plan to fix several of the tanker’s pressing issues, as well as how the aircraft can evolve for future missions.
The KC-46A starts out like other 767s on the company’s enormous Everett assembly line. Here, in the world’s largest building by volume, a 767 comes together, undergoing steps like fuselage and wing assembly all the way up to painting tails with customers’ preferred finishes.
On the line, the differences between a 767 freighter — passenger jet 767 deliveries have ceased in favor of newer models — and a nascent KC-46A are evident. The Pegasus’s complex military systems require much more extensive electrical wiring, a visible distinction in the fuselages of the two types of aircraft undergoing assembly.
After rolling off the Everett line, aircraft planned to serve as tankers are then sent to Boeing’s Everett Modification Center, where the company integrates military hardware like radar warning receivers and missile countermeasures that distinguish the Pegasus from its commercial counterparts. Here, Boeing also loads up the lower deck with box-shaped fuel tanks and equipment like the aircraft’s boom, furnishing the jet for its primary role as an air refueler.
Once finished, the tanker is then sent to its customer. The biggest buyer is the US Air Force, with smaller orders from Israel and Japan. Italy is reportedly in negotiations to join the Pegasus family as well.
From the balcony in the Everett Modification Center you can see most of the floor. There are more than a thousand people working here each day around the clock to build #KC46. pic.twitter.com/adfDS3LWyK
— Boeing Defense (@BoeingDefense) May 3, 2018
Walking through a KC-46A undergoing conversion work at the modification center, Breaking Defense was given an exclusive up-close look at an aircraft in this stage of production. Navigating through hot wires, open floorboards and racks of equipment, senior manager for KC-46A business development Mike Hafer pointed out the hardware that serves the tanker well — and didn’t shy away from where it’s gone wrong.
Seeing Clearly (With A Better Camera System)
Mounted on the underside of the KC-46A are two sets of cameras, each with distinct but similar tasks during all-important aerial refueling missions. One group of three cameras provides operators a digitally augmented panoramic view of the rear of the tanker to help them see aircraft approaching to refuel. A separate group of four cameras known as the Remote Vision System (RVS) narrowly focuses on the boom to help an operator guide it to a receiver.
Right now, both camera systems have problems. Specifically, the panoramic cameras can have difficulty detecting and identifying aircraft approaching for refueling under certain environmental conditions. The RVS cameras also struggle under dynamic lighting conditions, where nighttime refuelings can be hard to see or daytime runs can be washed out by bright sunlight. Depth perception issues with RVS further mean an operator is at risk of striking a receiving aircraft with the boom.
Problems with RVS’s performance have prompted Boeing to overhaul it with a successor known as RVS 2.0, meant to address an issue that officials have described as the greatest source of tension on the program between Boeing and the Air Force. RVS 2.0 consists of upgrading the aircraft’s two long-wave IR and two visible spectrum cameras and adding an additional set of visible spectrum cameras for a total of six.
The new vision system is expected to resolve two of the aircraft’s six category 1 deficiencies, which relate to visual problems for a boom operator and the separate risk of striking an aircraft. According to Hafer, a key change will come in installing more powerful video processors, a process that will also revamp the boom operator’s displays.
Each of the three existing infrared panoramic cameras will additionally be replaced with upgraded ones and supplemented with a new electro-optical sensor — in layman’s terms, a high-resolution, visible light camera — in a cost-sharing plan between the Air Force and Boeing, Breaking Defense has previously reported. According to an Air Force spokesperson, the service has separated the panoramic sensors out from the RVS 2.0 effort, and expects development of the panoramic upgrade to finish “after initial fielding of RVS 2.0,” currently expected in late 2025.
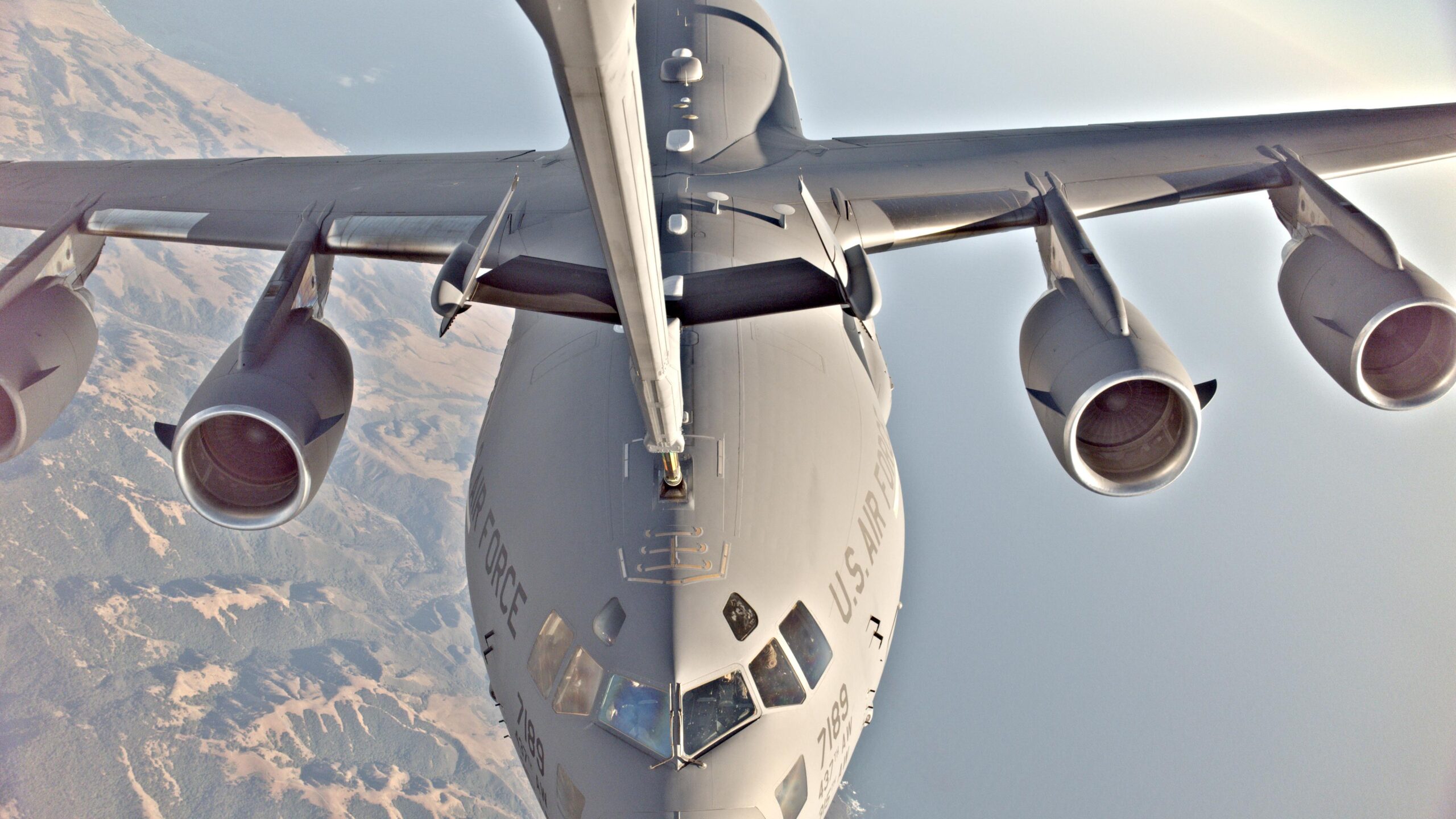
A two-dimensional representation of the 3D image boom operators will see in the KC-46’s Remote Vision System 2.0. (Boeing)
Into The Boom Shop
Around the corner from the KC-46A undergoing military conversion is the aircraft’s boom shop, where a small team of roughly two dozen employees takes about 40 days to complete a boom from start to finish, according to the shop’s manager, Luc Casagrande.
In the shop where employees were busy at work on booms in various stages of production, a fix for one of the tanker’s other category 1 deficiencies is underway. Currently, the Pegasus can’t refuel with the A-10 Warthog due to an issue with an actuator on the KC-46A’s boom — a small, U-shaped part that uses hydraulic force to extend a boom rod to a receiver.
The A-10’s relatively slow speed means it can’t generate enough force to stay connected to the boom rod with the current actuator in place, raising concerns that a Warthog could disconnect during a refueling attempt and put a pilot at risk. A new actuator offered by Boeing subcontractor Moog that is smaller, lighter and provides more dynamic force that can accommodate different aircraft is in lab testing, according to Hafer. The Air Force expects it to be fielded by fiscal year 2026, the service spokesperson said.
The boom production line has actually eschewed automation, Casagrande said, highlighting how four workers hand-drill about 3,000 holes for the boom. His small team means that workers can pick up right where they left off instead of risking miscommunications between changing shifts, he said, and that the shop is insulated from the pressures of the commercial business.
“We are 100 percent closed off,” Casagrande said. “This is our shop, our shift, and we put out the product that we like.”
Correcting ‘Product Quality’
After the two camera-related problems and the one involving A-10 refueling, the remaining problems with the Pegasus, known as “product quality” issues, involve three separate parts of the aircraft: drain masts for its auxiliary power unit (APU), a seal for its fuel manifold and a drain line that runs near the cockpit.
The problem with the APU drain masts — small metal tubes located near the tail of the aircraft that drain liquid — was that the tubes were cracking due to vibrations that had been overlooked during flight tests, Hafer said. Standing underneath the rear doors of the plane that the drain masts run along, Hafer noted that there was “stress” on the doors, which Boeing reinforced with additional bolting to reduce vibrations and prevent the masts from cracking. The masts themselves were also reinforced in the process.
“We said, ‘Let’s go ahead and just reinforce those critical areas.’ And that seems to have solved it,” he said.
In July 2023, Air Force program lead Col. Leigh Ottati said that the service was waiting to collect more data to ensure the fix worked as expected. Previously, Ottati explained, a similar category 1 issue with the drain masts was downgraded to a category 2 after Boeing rolled out a fix, only for the problem to return.
The fix for the drain mast cracks has been certified, the Air Force spokesperson said, and the service is “assessing design effectiveness through flight hour data collection.” Following quality assurance and the completion of retrofits expected by the end of FY24, the Air Force will close out this drain mast issue as a category 1 deficiency, they added.
A second product quality issue concerns the aircraft’s fuel manifold, which Hafer described as a “tube within a tube” that runs 555 feet throughout the plane and connects all the way from the refueling receptacle at the top out to the boom and centerline refueling drogue. Standing in the lower deck of the plane with the tube exposed, Hafer explained it has to be fitted with flex couplings throughout so that it can bend in flight.
The previous seal for the plane’s flex coupling on the manifold worked well when installed correctly, according to Hafer, though Boeing discovered that even some of the company’s own technicians couldn’t place it right. As a result, a gap could sometimes open that enabled fuel to seep out of the inner tube into the outer one, which collected in a sump below the plane.
So, Boeing implemented a new flex seal, part of a blue coupling placed periodically along the tube that Hafer said provides more flexibility. Retrofits are underway with the new seal for the whole fleet, which Ottati previously said should allow the deficiency to soon be downgraded from a category 1. A Boeing spokesperson said both the APU drain mast and fuel manifold seal fixes have been submitted to the Air Force for “down-grade and closure.”
“As of [Jan. 5], the solution is holding,” the Air Force spokesperson said when asked about Boeing’s fix for the fuel leak. The Air Force “will clear this CAT I DR [Category 1 deficiency report] once the remaining jets are through retrofitting. We are awaiting the maintenance facility timeline to accurately assess completion date,” the spokesperson added.
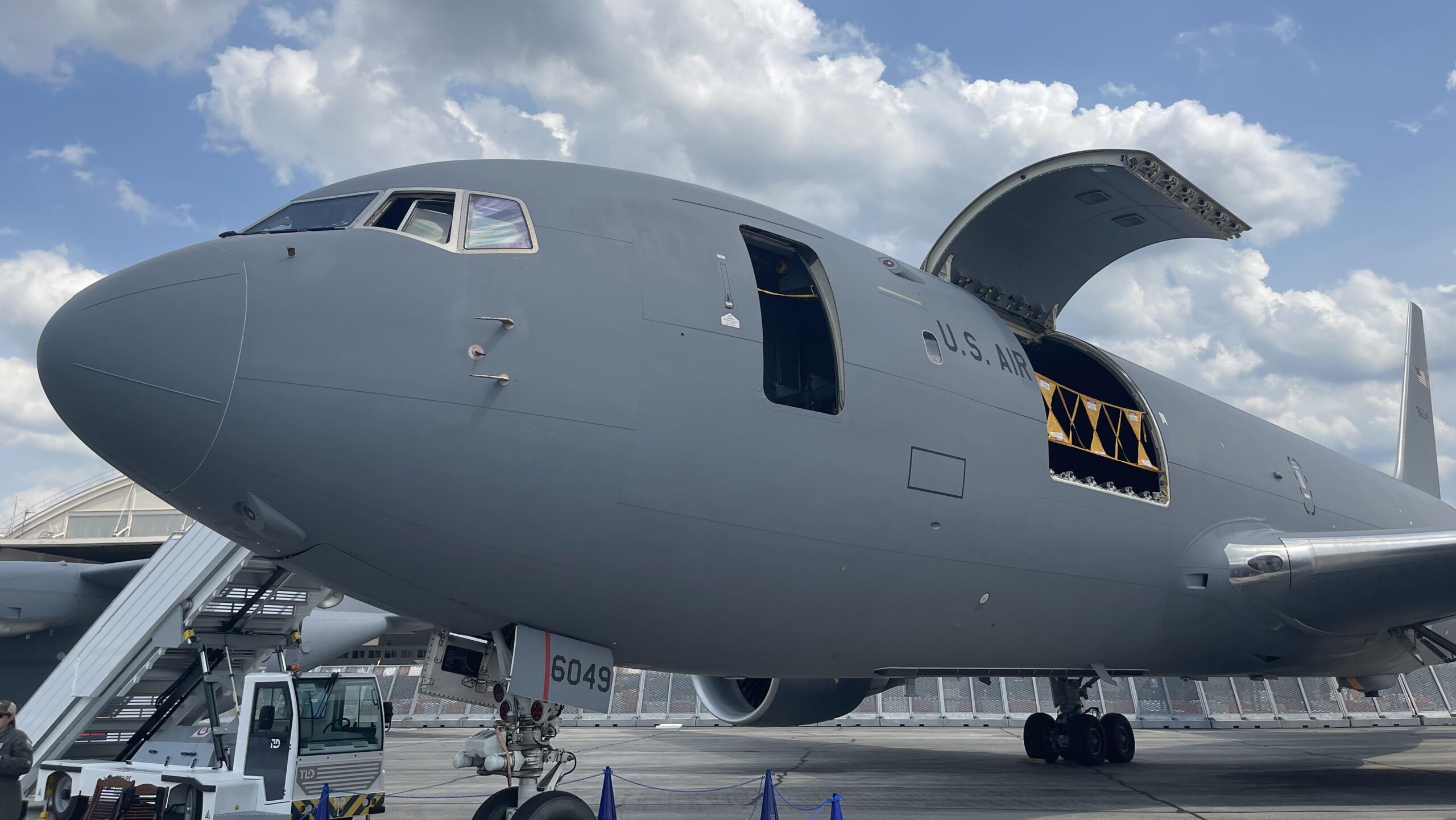
A US Air Force KC-46A Pegasus sits on the tarmac of the Paris Airshow with its cargo door ajar. (Michael Marrow/Breaking Defense)
In the aircraft’s upper deck where cargo, passengers or injured personnel can be carried, Hafer pointed out a small green hose near the ceiling of the airplane just outside the cockpit. This was the KC-46A’s third product quality shortcoming: the aircraft’s receptacle drain line, which empties liquid out of the tanker’s refueling port located on its crown. The line is at risk of cracking, which Ottati previously said could cause fuel to leak into the cockpit.
“The problem is there was a shallow run in there, so that if water was laying in there, it could actually freeze and crack,” Hafer said. A “workaround” that blasts air through the hose to clear it of liquid has been implemented until a new design is certified by the FAA, Hafer said, which consists of a “tube within a tube,” like the fuel manifold, that would be more flexible to prevent it from cracking.
The Air Force spokesperson said Boeing has finished testing “multiple design solutions” to fix the drain tubes, and the service expects to pick one of them during a program management review this month “or shortly after.” Once a design is approved, the Air Force plans to incorporate it in lot 8 deliveries starting this year.
Looking (And Flying) Forward
Should all these fixes pan out, Boeing might spare itself from more losses, though this year has been a reminder that not all financial risks are completely under the company’s control. For example, the Pegasus program’s most recent $245 million charge actually stemmed from a supplier issue, a problem that disrupted deliveries and contributed to Boeing falling short of an earlier goal to deliver 15 tankers to the Air Force in 2023.
“Following our recovery from a supplier issue, we communicated to the US Air Force that Boeing’s goal was to deliver 14 KC-46As in 2023,” a Boeing spokesperson said. “As a result of Boeing’s combined efforts with the US Air Force, we were able to deliver 13 KC-46As in the last half of the year, 12 to the US Air Force and 1 to Japan. We have more deliveries scheduled and anticipate that our delivery forecast will stabilize in 2024.”
And in spite of the KC-46A’s various issues, analysts told Breaking Defense they think it has a leg up against Airbus in a pending Air Force effort to recapitalize some KC-135 Stratotankers after Lockheed Martin’s surprise withdrawal. Winning that contract will likely help Boeing claw back its losses on the Pegasus program, though that work is still years away — current deliveries are scheduled through 2029, with efforts focused on fulfilling immediate orders like a $2.3 billion award from the Air Force in November.
The Air Force’s previous suggestion that it could go with an interim buy of 75 tankers for its recapitalization plan, where officials said that the KC-46A may be the answer, means that an “opportunity to make the program even more healthy from a financial perspective is in front of us,” Boeing defense business chief Ted Colbert told reporters ahead of the Paris Airshow in June 2023. The aerospace giant, Colbert said, is “all-in” on the KC-46A from the short to the long-term.
Even with all its issues, Hafer said he believes the Pegasus “outpace[s] anybody else out there in combat capability. And so if you really want a combat airplane, I’m not worried about the competition.”
Lockheed, Howmet settle lawsuit over F-35 titanium (EXCLUSIVE)
Lockheed Martin alleged in court filings that Howmet cut off the supply of titanium after the aerospace giant refused to agree to higher prices, threatening production of the F-35.