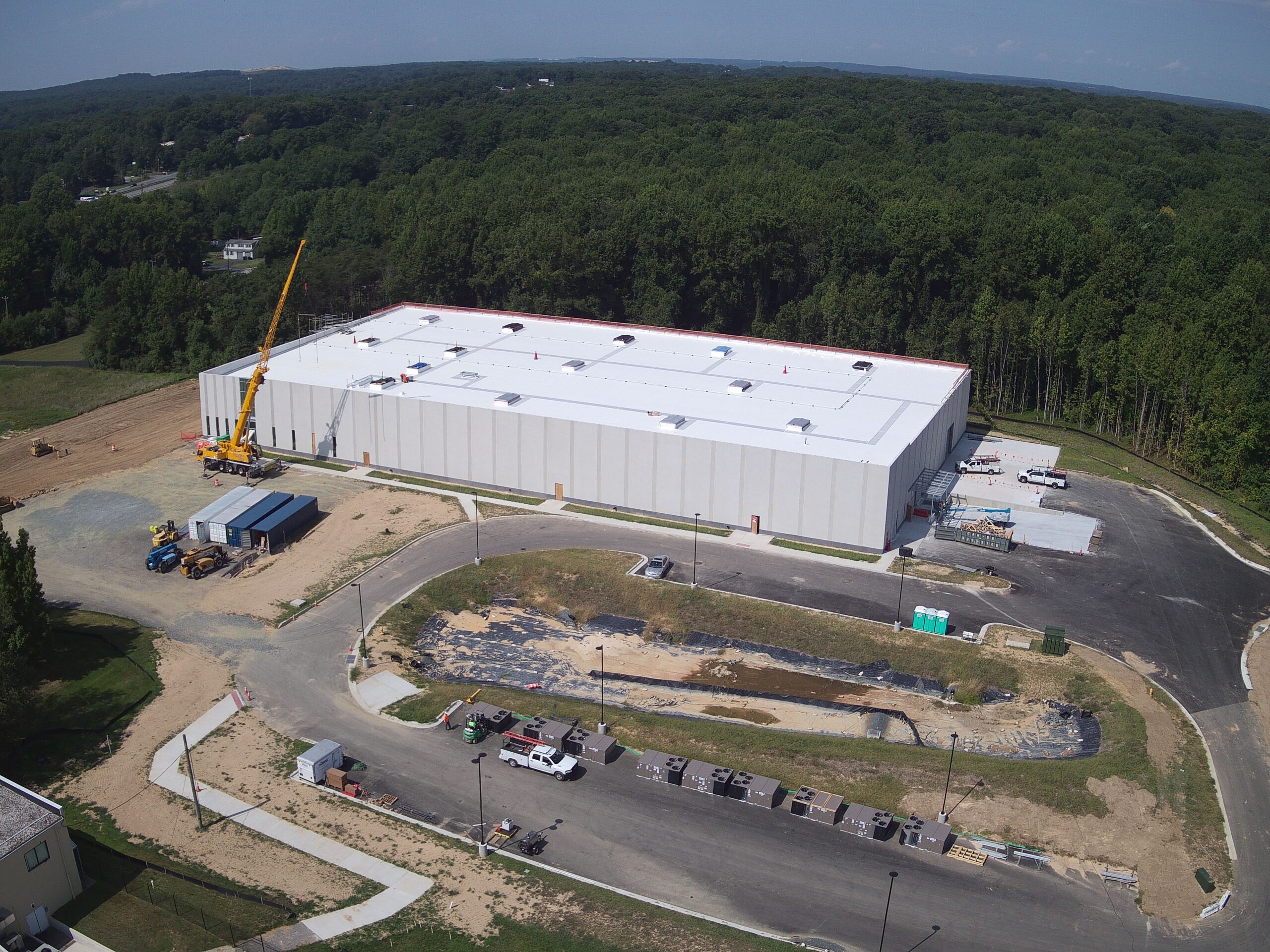
Aerial image of the Hypersonics Capability Center, which is designed to manufacture ramjets and scramjets in quantity for hypersonic weapons. Image courtesy of Northrop Grumman.
In this Q&A with Christopher Gettinger, director, Advanced Propulsion and Systems,
Northrop Grumman Defense Systems, we discuss how the company is investing in facilities and capacity to produce hypersonics affordably at scale; how it’s consolidating various actions and system providers to improve manufacturability; and what’s next for hypersonics.
Breaking Defense: We’re mainly going to be talking about air-breathing hypersonics in this conversation, but Northrop Grumman also develops propulsion for boost-glide solutions.
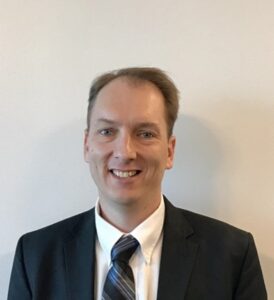
Christopher Gettinger, director, Advanced Propulsion and Systems, Northrop Grumman Defense Systems.
Gettinger: In the context of the advanced propulsion work that we do and the investments in facilities like our Hypersonics Capability Center, both air breathing and boost-glide hypersonic systems need propulsion during the initial phase to take them up to the operational speeds they require. We’re looking at the problem holistically and making sure that we’re addressing all portions of hypersonic propulsion. We’re not creating capability in one area while leaving a bottleneck in another capability.
Breaking Defense: Describe the threat scenario right now that necessitates the need for both types of hypersonics.
Gettinger: They bring different capabilities by nature of the way that they operate. With a boost-glide system, like the name indicates, you expend all your energy in terms of propulsion very early in the trajectory. From that point out, you’re managing the energy you have left with the glide vehicle as you’re going to a lower energy state over the rest of the flight.
The high speed and trajectory that you get with a boost-glide system allows you to fly a trajectory that’s different from a high-speed cruise missile enabled by scramjet propulsion.
On the air-breathing side, the main difference is that we boost it up to a given speed during the initial phase and then maintain that speed or energy state across most of the trajectory. It’s the difference between the two that allows you to use them in complementary and different roles. Since the scramjet system uses air as its oxidizer, those systems can generally be packaged in a smaller package. We can effectively fit more systems on a given platform.
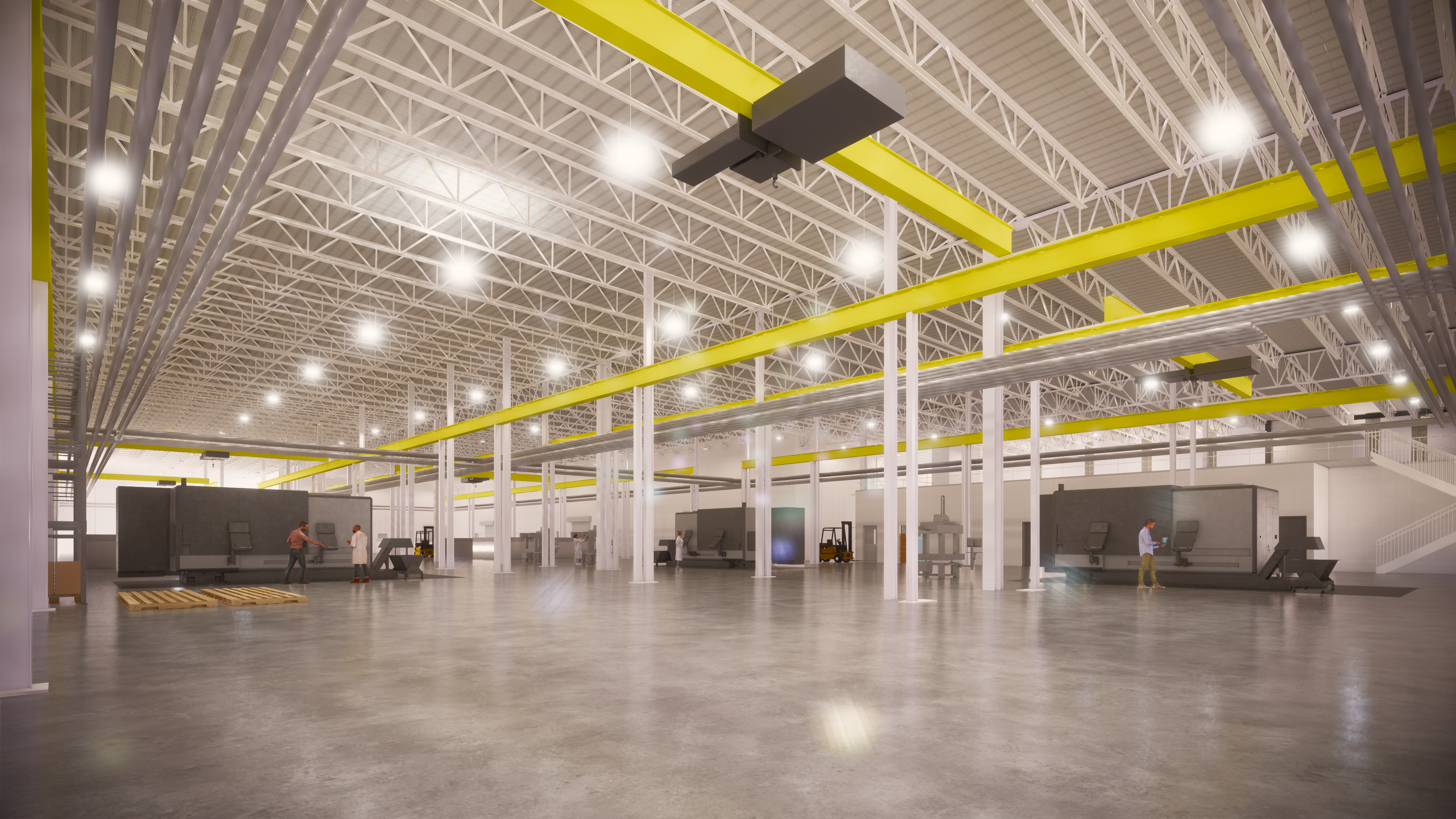
Artist rendering of the Hypersonics Capability Center interior. The scramjet factory is Northrop Grumman’s first in the U.S. Image courtesy of Northrop Grumman.
Breaking Defense: How have you met the challenges associated with hypersonics at scale, which is having the ability to produce them affordably and in large enough numbers to make a difference? Also, how do you attract people with the skill sets you need in areas like high-speed flight engineering, for example?
Gettinger: There are several facets to it, and we inject innovation at every turn. We have consolidated various steps within the system itself, and have gone through the entire process to design for manufacturing affordably at rate. When we build prototypes we may use a particular manufacturing method or source that’s expedient but perhaps not the most cost effective. When we start thinking about making these systems at production-level rates, we go back and look at a couple of things.
First, are there new or advanced manufacturing capabilities that have come online that we want to apply to these systems to help us produce at rate? Second, and just as important, are there existing low-cost and proven manufacturing techniques that we want to apply that may be different from the prototyping techniques?
Often those types of techniques require some amount of manufacturing development and investment before you can produce products at rate. Think about traditional low-cost processes like casting or sheet-metal forming. Once the investment is made to make the specific tooling that you need to produce products at scale, you can then produce them very affordably. So design for manufacturability and affordability is the critical element to facilitate high rate production.
Once we’ve set the manufacturing needs, we then streamline the supply chain. Often we’re looking for ways to consolidate various actions or manufacturing steps, and to work with fewer providers or to bring them in house at times and consolidate them internally.
We’re ensuring that we don’t have single points of failure in our supply chain. We also push down some of the digital engineering and manufacturing methods to our suppliers to ensure that they can help us produce high-quality products affordably.
Pivoting to the workforce, we look ahead to ensure we retain the workforce to the degree possible, and also ensure we’re building the workforce needed for the future. This means finding the proper skill sets to match the manufacturing methodology.
In addition to the workforce, we’re pursuing investments in our manufacturing facilities. Our Hypersonic Capability Center in Elkton, Maryland, that I mentioned earlier is designed to help us manufacture these types of air-breathing systems — ramjets and scramjets in quantity — to use for these types of weapons.
Breaking Defense: How is Northrop Grumman investing in facilities and capacity to produce hypersonics affordably at scale and rapidly deliver capability into the field?
Gettinger: That’s really the cornerstone of those capabilities. The bottom line is that we didn’t have a ramjet or scramjet factory here in the U.S. that was able to produce these at high rates. In many ways, there are benefits to custom build a facility for ramjet and scramjet production where you can get exactly what you need through careful planning.
In addition, we took a top-to-bottom look at the production capacities we have in our existing facilities in order to identify bottlenecks in the process. We’ve invested in very specific areas to ensure that we’re addressing those so we can continue to produce our current product lines and also produce enough units to satisfy the needs for both boost glide and hypersonic cruise missile systems.
Breaking Defense: What are the technological and manufacturing challenges associated with the advanced materials and thermal management required for hypersonic weapons?
Gettinger: Certainly thermal management is a key to this. I mentioned the different ways that boost glide systems and hypersonic cruise missiles are employed and each have their own unique challenges.
Boost glide systems, because they expend all their propulsive energy early in the trajectory during the initial phase, meet much higher peak speeds and higher peak temperatures than we generally see on hypersonic cruise missiles. That means they’re going to drive to a very specific set of material requirements. At different points in their trajectory, they may see lower heat loads or very high heat loads. So, you must design for not only higher peak temperatures, but a broad range of temperature and heat-load conditions.
With hypersonic cruise missiles, again, because we’re powered throughout using scramjet or ramjet propulsion systems, there’s generally less variation in the peak temperatures. While we don’t see as large a variation, we may see a larger integrated heat load that we have to manage for a longer time because of the differences in how the systems fly.
Breaking Defense: What’s next for hypersonics?
Gettinger: We must turn the corner and move away from the work we’ve done building and demonstrating prototypes and move toward a large-scale manufacturing capability. A lot of our focus is on that. We also continue to innovate on air-breathing and boost-glide propulsion such that we can develop capabilities for our next generation of these systems.
For example, boost-glide hypersonics drives the need for us to minimize the amount of inert weight on a rocket motor system and maximize the amount of impulse that we can get out of it. We have several key advanced-solid-rocket-motor technologies that we are pursuing to help us do that. We want more propellant in a system and to get a lower mass fraction of inert into the system, including moving to more advanced materials. Northrop Grumman has been in this business for many years, and we have our own test and production facilities for air breathing and rocket propulsion for the military.
We’re investing heavily in our infrastructure to make sure that we meet future requirements of our customers regarding air-breathing and boost-glide hypersonics propulsion.
We’re also investing in talent — to not only attract the best talent, but to retain the talent we have now.
Our long history and good relationships with customers helps us to better understand their needs. We don’t develop systems looking for a problem. We go to the customer, understand their problems, and then develop the best solution to meet those needs.
Our intent is to gather information on what the customer thinks they’re going to need five or 10 years in the future and make sure that we’re developing systems and new solutions that enable them to meet their objectives.
Then finally, we have the capability to ramp up production. We are actively and heavily investing in that as we speak to meet near term-needs.