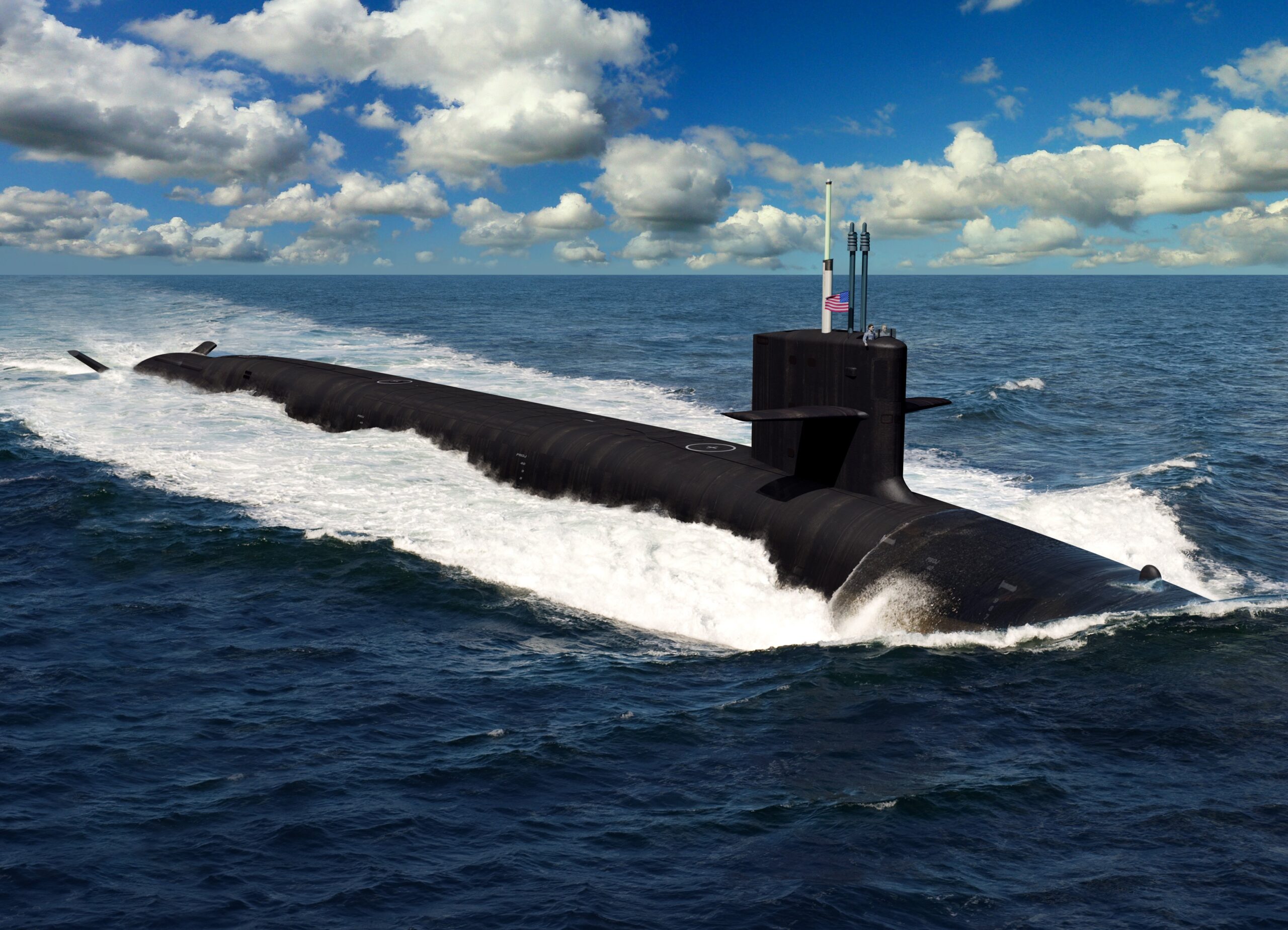
The Columbia-class ballistic missile submarine, shown in an artist’s conception, will have an electric-drive power-propulsion system developed by Leonardo DRS. Photos courtesy of Leonardo DRS.
Technological change in the form of electrification for propulsion, advanced radar, and directed-energy weapons is becoming an essential ingredient in Navy shipbuilding. Requests for proposal increasingly include requirements for fully electric vessels across naval ship classes from next-generation guided missile destroyers like the DDG(X) to the newest class of ocean surveillance ships called T-AGOS 25 for anti-submarine warfare.
In December 2021, for example, the Navy issued a final RFP for the design and build of the T-AGOS 25 class, which will include electric propulsion for more silent operations and greater speed to quickly reach hot spots across vast ocean distances in order to gather undersea acoustic data from its towed-array sensor system.
To execute these varied programs, the Navy is looking for a company with both reliable technology and experience electrifying ships. Leonardo DRS — as the electric-propulsion provider for the U.S. Navy’s Columbia-class submarine, the South Korean Future Frigate eXperimental (FFX) program, and the U.S. Coast Guard’s new fleet of Offshore Patrol Cutters — brings both reliability and experience to the table.
In this Q&A, we talk with Clive Wilgress-Pipe, senior director, strategic programs and business development, Leonardo DRS, about electrification on the DDG(X), lessons learned on the South Korean frigate program, and the importance of having a single system vendor to work with the shipyards on electrification.
Breaking Defense: What capabilities will electrification bring to the U.S. Navy, and specifically to the eventual DDG 51 replacement, the DDG(X)?
Wilgress-Pipe: The primary driver is definitely electric weapons, whether they be lasers, more powerfu radar, and other weapon systems down the road. The DDG-51 Arleigh Burke-class destroyer is the US Navy’s primary surface combatant and has been continuously upgraded over the class’ lifetime, but is likely reaching the point where the platform needs to be replaced for the US Navy to maintain its global surface combatant edge.
A few years ago, DDG-1000 was planned to be this vessel with an integrated electric drive propulsion system. However, there were challenges to the program including technical problems with some of the advanced technologies that were installed and it was very expensive to build. The program was cut to three ships and it has not been deployed as a combatant in the active fleet.
Going forward, however, the Arleigh-Burke class, as well as the Ticonderoga-class cruisers, will eventually have to be replaced. The Navy is now looking again at a fully integrated electric drive solution to give them the power flexibility that they desire. The Navy has indicated that the coming DDG(X) will be an electric-drive platform with a high voltage distribution system when the RFP eventually comes out.
That being said, what does the Navy really want? They want a destroyer-type vessel that is a superior and cost-effective replacement for the Arleigh Burke-class, and they want it to be equipped with the latest radar and weapons, along with full-power flexibility for those systems.
A few years have passed since DDG-1000, the state of technology has advanced, and the Navy did not lose faith in the concept. We are providing electric drive on the Columbia-class submarines, and full-power testing has already been successfully achieved, essentially proving the concept. This was not the case on DDG-1000. For DDG(X), we will leverage our Columbia experience to provide a proven and reliable system for the surface Navy.
The US Navy PMS 460 program office, which is in charge of the DDG(X) next-generation destroyer program, is casting its net wide to find the capabilities that industry has to offer. They’re deciding on final configuration now, and, of course, Congress is actively involved in this process, as well. Congress wants the Navy to thoroughly prove and test the system before construction begins, a lesson learned from the DDG-1000. The Navy will make technology selections and undertake integrated testing to prove out all the major items before they award the contract to construct the class.
Breaking Defense: I would say that’s a good thing.
Wilgress-Pipe: Yes, for both our nation’s security and for us as taxpayers, it’s a great thing! Leonardo DRS is going to do everything to help the cause by leveraging the heck out of our proven references on Columbia and the in-service Korean FFX hybrid electric drive frigate program, as well as work that we are doing to prepare for T-AGOS.
The T-AGOS 25 program is being bid right now. The propulsion motor for that would be less powerful than for DDG(X), but would be selected from our same class of machines. Leonardo DRS has a common frame size structure for our advanced permanent magnet machines, so the T-AGOS 25 motor, when fully tested, would be an excellent de-risker for DDG(X) because it would essentially be the same motor, only longer.
Hence, we could de-risk DDG(X) and provide the most cost-effective solution for the Navy by leveraging what we do on the T-AGOS 25 program.
Breaking Defense: So far, there are four of eight FFX-II Daegu-class guided-missile frigates in service now with the Republic of Korea (ROK) Navy. What lessons learned are there regarding electric propulsion on those vessels that might be of interest to the US Navy?
Wilgress-Pipe: It’s been a new experience for the ROK Navy because traditionally their ships have been mainly traditional mechanical propulsion, similar to the U.S. It’s also been a new experience for the shipyards. One thing that’s come out of it — and this is definitely going to also be the case with the shipyards here in the U.S. — is the need for a strong integrator to pull all the pieces together.
For the most part, the shipyards don’t have experience with electric drive. That means their engineering departments sometimes don’t know the right questions to ask and exactly how to even specify the equipment. As a result, we’re seeing a general drive toward having what’s being called an SSV, a single system vendor, to provide the electric propulsion package as a subcontractor to the shipyard.
An SSV is required by the Navy on T-AGOS 25; the RFP specifies that the shipyard has to partner with an SSV for the integrated electric drive propulsion system. The SSV will be responsible for specifying and integrating the whole thing from the gas turbine generator and diesel generator sets, through to all the electrical parts, power distribution system, drives and motors, all the peripherals, as well as the control system that makes it all work together. Even the mechanical shafts, propellers, and shaft bearings are included in the package. The SSV is directly responsible to the shipyard to make sure that the entire propulsion system is specified correctly and integrated.
A similar approach is being taken for the ROK Navy’s new KDDX program (a stealthy, smaller, guided missile destroyer), as well as their new CVX light aircraft carrier. Following on from T-AGOS, the US Navy will likely continue with this arrangement. The SSV approach takes a risky burden from the ship builder and reduces that risk for the end user (the Navy).
In summary, I would say that an important lesson learned is that there is significant risk reduction and advantage to the program and end user by pairing a competent systems integrator with the shipyard from the outset of the program.

The Navy installed an Energy Storage Module on the USS Portland (LPD 27) to support the Solid State Laser. Shown are sailors and marines preparing to launch two landing craft from the well deck of the USS Portland. Photo courtesy of US Navy.
Breaking Defense: Let’s talk a little bit about why you feel that Leonardo DRS has an advantage over other competitors in this market. What makes your systems and your company special in this area?
Wilgress-Pipe: We are the only entirely US designer and builder of these systems. Everybody else imports pieces from outside the US. We build the motors, drives, and control systems here in the US. We’re unique in that area, as far as the US Navy market is concerned. We have leveraged that US-based experience to help our US allies, particularly the RoKN, that typically adheres to US MIL-STDs.
We’re a US company, all of our engineering teams are here, and we are leveraging our primary two references — the COLUMBIA propulsion system, which is essentially the most advanced integrated electric-drive system in the world, and the RoKN FFX propulsion system — as we go forward from T-AGOS to DDG(X). It’s a unique combination that benefits the US Navy in terms of responsibility, technical superiority, risk reduction, security, and speed of response. Of course, other companies have references, but the knowledge base that goes with ours is here in the USA, which will be singularly helpful to the US Navy as it moves full-ahead into the electric-drive arena.
Breaking Defense: What makes the COLUMBIA electric drive system the most advanced in the world?
Wilgress-Pipe: Well, you understand that I am unable to provide any details about that reference system. I will say that it is an advanced multi-megawatt system, where the components we’re making are required to have a 40+ year service life, and most of the components are required to have that life with essentially zero maintenance.
What is at the heart of our electric drive systems is our proven permanent-magnet motors. We know with certainty that we can build the most reliable and rugged permanent-magnet motor for the US surface navy because we’ve already done it for the subsurface navy.
There are many technologies that go into our solutions to make our propulsion systems acoustically superior. That’s an important element that the surface navy is looking for to develop and field effective anti-submarine warfare (ASW) platforms and, again, our subsurface experience helps us to provide quiet solutions.
All the other navy’s in the world, of course, continue to advance, as well, both friend and foe. Certainly, new surface vessels for the US Navy and our allies must be designed and built to be as stealthy as they possibly can be to avoid detection by Chinese and Russian submarines, while at the same time being able to effectively find them. Hence, there’s a lot of emphasis on acoustic performance, noise control, and sensitivity in detection systems.
That’s another driver for and capability of electric-drive propulsion systems. When properly designed and built, electric drive is fundamentally quieter than traditional mechanical drive.
Breaking Defense: Final thoughts?
Wilgress-Pipe: The US Navy is making a considered and wise choice to push ahead with electrification, both for propulsion and for weapons. It’s going to give them superior firepower, more flexible CONOPS, longer duration, and more reliable systems. Electric drive systems require less maintenance because, fundamentally, there is less maintenance required on electric components than for mechanical ones.
So, what does that give the US Navy? It means they are going to be quieter and less detectable at sea. They are going to be able to find opposing combatants more easily, have more firepower flexibility when they get there, and they are going to be able to stay on station longer than they could with traditional mechanical propulsion solutions. It’s a win-win situation.