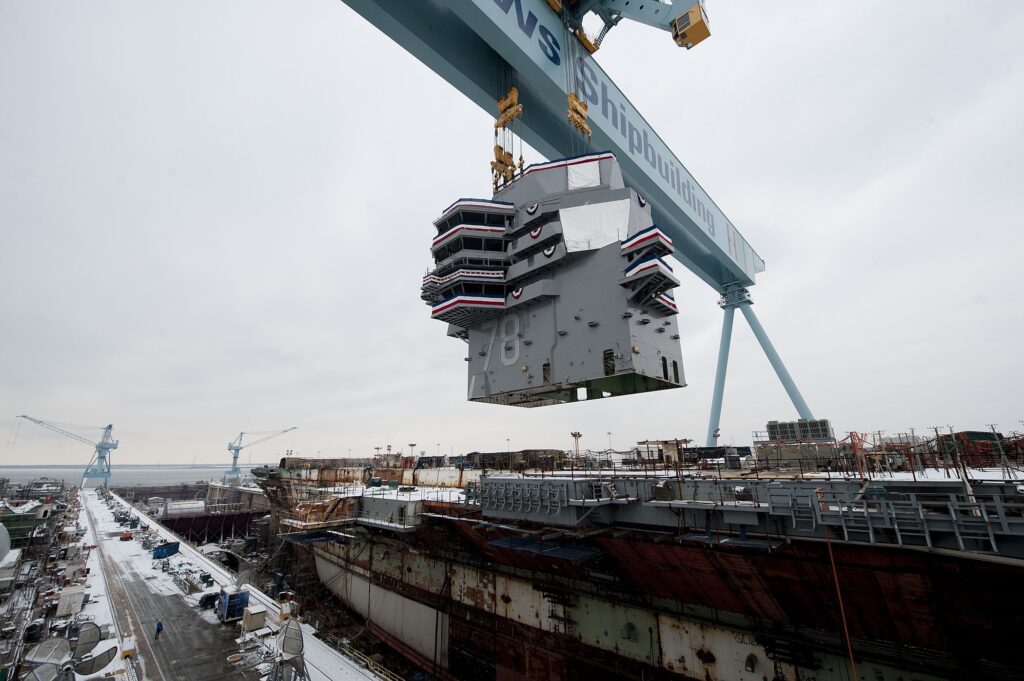
The nuclear carrier USS Ford (CVN-78) under construction at Newport News Shipbuilding.
The world’s only builder of nuclear-powered supercarriers is investing $1.8 billion in its shipyards through 2020 to help the Navy grow to its target of 355 ships, including 12 carriers. Huntington-Ingalls Industries’ investment includes new digital technologies to streamline traditional heavy labor like welding steel and running cable.
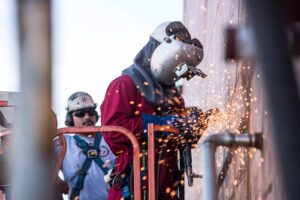
Newport News workers build the future supercarrier USS John F. Kennedy (CVN-79)
The Navy’s new acquisition chief, James “Hondo” Geurts, was impressed by HII’s high tech tools during a visit to the company’s giant Newport News yard in Virginia. Newport News builds all nuclear-powered carriers and half of the Navy’s nuclear submarines. New England’s Electric Boat, owned by General Dynamics, builds the other half of each sub; the two yards ships components back and forth on huge barges.
Huntington-Ingalls’ other major yard, its namesake facility in Ingalls, Miss., builds conventionally-powered destroyers and amphibious warships — competing with General Dynamics’ Bath Iron Works in Maine and NASSCO in San Diego — as well as the Coast Guard National Security Cutter, a version of which HII’s proposed as the future Navy frigate.
While HII wouldn’t give precise figures, about $850 million of investment is going into Newport News and $950 million into Ingalls. The company’s original 2016-2020 plan called for $1.5 billion roughly equally between the two yards, CFO Chris Kastner explained to me ahead of the annual Sea-Air-Space conference outside DC, but an additional $300 million announced this year — in response to Trump’s tax cuts and Navy expansion plans — will be split 1/3 Newport, 2/3 Ingalls. If the Navy increases submarine from two to three boats a year, as it hopes to do, the company would need to invest even more in Newport, Kastner said.
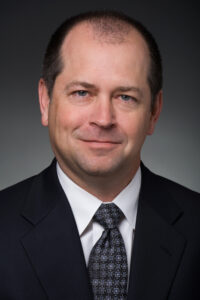
Chris Kastner
Much of the money goes to hangar-like buildings that can enclose multi-hundred-ton sections of a ship or sub so as much work as possible can be done inside. For outside work, there are mobile tent-like structures called Rolling Bay Covers that move to protect the workers wherever they are. Imagine trying to weld steel in the pouring rain and you’ll understand how this improves productivity. The goal is to build as much of the vessel as possible in pieces under factory-like conditions, then put these modules together into an actual ship and add only the finishing touches outside.
Huntingon-Ingalls has also invested in replacing traditional paper plans with digital ones. First, Kastner told me, electrons are a lot more practical to carry around. A tablet can carry the same amount of data as a bulky box full of paper. Second, the tablets make it much easier for workers to cross-reference between the overall design, the detailed instructions for what to install where in what order, and other technical data.
“They can see the design, they can see the sequencing, they can see the specifications, and it’s all right in front of them in 3-D,” Kastner told me. Digital tools are especially helpful, he said, for planning out the work and preventing costly mistakes.
That’s a big deal considering that if you weld something in the wrong place or wrong angle, or thread electrical cable through conduits to the wrong place, it’s going to be much harder to undo and do over than it would have been do it right in the first. While Kastner didn’t say so explicitly, this kind of digital guidance will be especially helpful for the many young, inexperienced workers the yards have had to hire in recent years as they grew to meet the Navy’s needs — and the big advantage these younger workers have is that they grew up with this kind of digital technology.
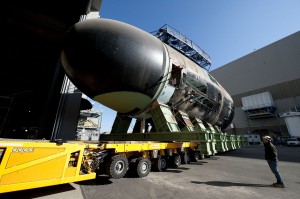
The USS Warner under construction in Newport News, one of the last two shipyards in the US able to build a nuclear-powered submarine.
Huntington Ingalls is also experimenting with augmented reality goggles that would superimpose digital plans on the wearer’s view of the real world, letting workers see exactly where the next part should go. But augmented reality is still an early pilot project rather than all-out push like digital plans on tablets.
The yards are also exploring automated welding, and Kastner predicts that in the long run, most welding will be computer-controlled. That said, however, there’ll still be plenty of human talent involved in setting everything up in the right place so the computerized welding tools can work. Other crafts may be harder to automate, he said.
“Each of your crafts — electrical, pipefitting, pipe-welding, painting, your riggers… still require some human touch,” Kastner told me. “Digital tools… free the craftsman up a bit to not do the grunt work.”
Shipbuilder Austal USA names Michelle Kruger as new president
Kruger had been serving as interim president since former chief Rusty Murdaugh resigned last spring.