
Bell’s focus on digital design and development reduces risks by iterating and maturing designs for both the FLRAA and FARA programs. Photo courtesy of Bell.
In this Q&A with Becky Stiles, director of Vehicle Systems at Bell, we discuss how the company’s focus on digital design and development reduces risks by iterating and maturing designs in a fully integrated aircraft-representative lab for both the V-280 Valor for the Future Long-Range Assault Aircraft (FLRAA) program and the Bell 360 Invictus for the Future Attack Reconnaissance Aircraft (FARA) program.
Breaking Defense: Tell me about Bell’s focus on digital design and development and how you’re applying that to the Army’s FVL modernization plans?
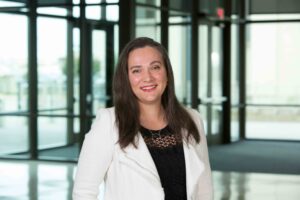
Becky Stiles, Director of Vehicle Systems at Bell.
Stiles: In the past few years the Army has been clear that FVL programs are critical to maintain the U.S. military’s dominance by radically improving upon the current fleet’s speed, range, agility, power, durability, versatility, and sustainability. Our team firmly believes that developing, and fielding survivable, highly capable, and forward-looking platforms is part of the equation to successfully modernize Army aviation. We are also applying best practices and processes learned through our commercial development cycles and technologies to improve affordability, sustainment, systems integration, and manufacturing.
A large part of my work is focused on developing these new weapons systems in wholly digitally connected environments, often known as digital threads. This methodology connects all aspects of program development from initial design to verification that will make the V-280 Valor and Bell 360 Invictus combat ready through the efficient integration of mission equipment, avionics systems, and all the required software packages needed to qualify a safe and effective aircraft. Sustainment is also a major opportunity area to make sure we’re getting the right data to the Army so they can understand and effectively manage their fleets using a data-driven approach.
Model-based systems engineering is an example of where we use digital threads, and we are receiving requirements from the government in a digital model and in turn deriving functional, performance, and interface requirements within the common digital environment.
For example, in the ideal mode-based scenario, if you have to swap out an engine or a Line Replaceable Unit, you have your input/output mapped. You’re not relying on interface-control documents that are in paper form, and you don’t have to ensure that your configuration management is caught up because it is all captured digitally within the model.
Our suppliers are in the computer-aided-design environment with us designing alongside our team. There are numerous hardware systems such as airframe, drive systems, and wire/tube routing that are all maturing in parallel and transparently across the integrated product teams (IPTs). As we’re maturing the design we want to make sure the hundreds of engineers are all in lockstep with each other; that is the uniqueness of the digital tools we have today as opposed to those used during the design of enduring fleet aircraft.
That is a key benefit of this methodology. As we are maturing designs, our suppliers, and teammates, as well as the Army, are in the same environment with us. As risks are identified, we can work them in real-time, regardless of physical location, and don’t have to conduct analysis separately. We improve overall affordability and speed to first unit equipping by working with an agile process that allows us to resolve issues in real-time, which is faster than the traditional waterfall method used in previous programs. This digital environment and these digital threads allow us to work concurrently together as we iterate and mature designs and requirements in an organized and data-driven manner.
Breaking Defense: If you don’t have time for waterfall, then that means you’re using agile systems development?
Stiles: Correct, it allows us to close the loop all the way up into the user community to ensure we are meeting requirements. If we identify a requirement that they would like modified, we can quickly and accurately give them the impact of the change.
The focus of our engineering and systems integration lab teams is on meeting the customer goals in how they use their platforms for operations. We’ve seen that as they become familiar with the capabilities of FVL aircraft, they learn to do more and learn they want to do more. We can immediately put that thinking back into our digital thread and model and see what the impacts are going to be through the lab. Or, if they need to do an upgrade, we can either give them that capability faster or we can start testing to explore the ability to expand the envelope from our original requirement.
During the Joint Multi-Role Technology Demonstrator (JMR TD) program there were several avionics-upgrade cycles being worked with our Team Valor teammates, such as adding in the Pilotage Distributed Aperture (PDAS) system, a Tactical Common Data Link (TCDL) along with several software improvements related to pilot situational awareness and experience. All of these upgrades were accomplished within the period of performance involving the test teams working in concert with our engineering teams to efficiently verify safety and performance through testing, flight rehearsals, and test card development.
We’re both bound and inspired by the Modular Open Systems Approach (MOSA) requirements—the FVL Architecture Framework, the FAF. We are deriving standards from the FAF and putting those into our system requirements and pushing them out to our suppliers. That allows us to build in growth opportunities, upgradability and capability while also providing off-ramp paths for obsolescence up front, saving time and money on the back end for things like regression testing.
In the past, developing a software upgrade would be fairly expensive because you would have to qualify the entire integration tail that went along with it. Now we are able to package the software and hardware in such a way that we understand where those integration boundaries stop and start, allowing the customer and us to compartmentalize and get the Army the capability they need faster and more affordably.
What we did with the V-280 during flight testing is a good example. We got that demonstrator flying with our fly-by-wire flight-control laws, which will be a new capability for Army aviation. These systems provide increased safety, agility, and mission performance for the operational community. We were able to keep iterating those control laws—increasing the levels of augmentation to improve handling qualities as we progressed through the flight envelope, which included an autonomous flight. We’ve proven we can iterate effectively and efficiently in the lab first with the pilot in the loop and then move it to the aircraft safely.
Breaking Defense: How does program performance on the ground that you’re describing impact the Army mission?
Stiles: First and foremost, they need the product to be able to execute their mission. That is what we are extremely focused on, building a relationship with the Army so we always understand the why. If we understand the end goal, we work with them and utilize Bell’s demonstrated experience to get into the what and the how.
Bell is investing in two major efforts because we believe so strongly in the mission of affordable execution and we need to have the infrastructure in place to execute. The first one is the Drive Systems Test Lab. The second is a new purpose-built weapon system integration lab for FLRAA and FARA. The labs will contain enough space and provision for drive stands, electrical power, test benches, classified systems, and much more to ensure a thorough and aircraft-representative environment where we are able to quickly identify integration issues and verify fixes. We have shown the benefit of speed to the upgrade within those labs for the V-280 during JMR TD that leads to a more affordable model moving forward.
Breaking Defense: So, what’s the why, what, and how for FVL?
Stiles: The “why” includes the requirement for the Army to modernize its aviation forces for the first time in more than 40 years in order to maintain dominance in this environment of Great Power competition and ensure global relevance at the speeds and ranges required of multi-domain operations. And then sustain that dominance by giving them the ability to affordably upgrade capability over the lifecycle to stay ahead of our near peers.
The what and the how are where we leverage the digital enterprise upon flight-proven tiltrotor and helicopter air-vehicle configurations. Having a collaborative, trusting relationship with our teammates, suppliers, and the Army lets them bring us their roadmaps so we can incorporate them in our models early on to identify risks. We don’t need them to provide the answer; we will use our models to tell them where there may be physical or data bus clashes between systems and then take it to our lab for testing and qualification.
The systems integration labs (SILs) are really the key to what we’re doing. Having the actual flight controls and actuators in the lab lets us address human factors extremely early in the process. To speed the iteration of software, we have benches that allow us to develop solutions with partners like Moog, Lockheed Martin, Astronics, and Rolls Royce, and to insert upgrades and acquire the customer’s subjective, operational feedback. The labs also allow us to tie the mission systems to our flight controls and avionics, allowing us to bridge the gap to autonomy much faster.
We go through the loop of idea-to-iterate-to-validate to get a capability on the aircraft or in the program much more efficiently and affordably so we can drive down program costs from the outset. And then in terms of reliability and safety—all the airworthiness qualification levels we need to address—we can do much of that in that digital environment before we ever have to put something on an aircraft. We know that once it leaves the lab that modifications get more expensive, so we drive down the risk as much as possible before it ever leaves that environment.
Breaking Defense: FVL is the Army’s first program to develop fly by wire aircraft. How are you working with them to bring a level of comfort to this major shift in air operations?
Stiles: It’s important to remember that the Army hasn’t developed a clean-sheet rotorcraft in decades. The Black Hawk was designed and built in an analog world; there was no digital world. This is an opportunity for the Army to become comfortable working in a digital environment for the lifecycle of a program and realizing the benefits of iterative design and upgradability.
For example, throughout the JMR TD initiative our engineering team worked in our SIL along with the pilots and test team; then the pilots went out and executed. We were reactive to what they experienced, we went and expanded the flight envelope in the lab, and then we tested it again to make sure that it continued to perform safely and better than before.
Fly-by-wire is all about reducing pilot workload whether it’s hover-hold or quick maneuvering. So that iterative process that I’ve described starts off with getting the aircraft in the air safely and then starting to increase those control laws to reduce pilot workload, allowing them to fly faster, have all the required maneuverability at their fingertips, and focus on executing their mission.
Breaking Defense: How are you using these digital capabilities you’ve described for sustainability, particularly for predictive maintenance?
Stiles: This is another way that digitization of a program benefits the Army—by making maintenance predictable. This lets you concentrate on anomalies more, as opposed to concentrating on all the data. It’s a different approach to maintenance than what Army Aviation takes right now, which is pegged to flight hours rather than actual wear and tear on a component.
Data analytics is a big part of this. We’ve partnered with GE for the Integrated Vehicle Health Management System. We’re leveraging lessons learned from our commercial aircraft to incorporate fly-by-wire flight controls, and GE is leveraging commercial lessons learned in their fixed-wing fleets. We’re putting those together to develop algorithms that not only make sense now but also algorithms that will learn and improve as we go forward.
I always say that data for data’s sake doesn’t do anyone any good. The Army wants, and we have to have the ability to look at that raw data, understand what we’re seeing, and bring options forward to them for quick and effective integration into their existing infrastructure. As I mentioned earlier, they will learn new things as they fly the V-280 and Bell 360. And we will find new ways to inform on how to maximize the aircraft now and evolve it for the future.
Breaking Defense: How will the digital thread reduce risk for Army FVL?
Stiles: Through the JMRTD program, we’ve demonstrated that we can proactively manage risk, expand capability, and deliver stronger outcomes for our Army partners. We will continue to do that and expand our virtual and our digital capabilities.
The key is identifying the risks and prioritizing requirements challenges as early as possible, and then activating corrective-action plans that come from a holistic operational perspective for both hardware and software. The sooner we can get items into the lab with the customer, the better off we’re going to be.
Everything is in alignment with the Army’s timeline for Engineering and Manufacturing Development, First Flight, Testing, and First-Unit Equipped phases. We are already in those digital environments with the Army and our partners working toward program-of-record-level development.
Breaking Defense: Final thoughts?
Stiles: Bell understands the need to get the capabilities of FLRAA and FARA into the warfighters’ hands. That, I believe, is another big part why Bell is positioned well to partner with the Army. We really understand the need and the why, and we believe in the mission.
The role of digital models and the digital thread are critical to providing the Army with transformational capability. However, it is important to emphasize that all the modeling helps get us to the flying and sustaining of an aircraft. We proved the value of the digital models through flight test of our V-280 demonstrator and soon with the Bell 360. In the end, it is the physics of the weapon system in test and in operations that will ensure it meets the needs of the warfighter and our digital methods are a means to that end.
To do that we have embraced and internalized in our processes and in our relationships the need to model and drive out risk early. Whether it’s in the physical structures or in the hardware and software components, everything is being developed with that in mind in order to quickly identify opportunities to make first flight in 2025.
Finally, Bell’s investment in the workforce is incredibly important to this. And it gets back to understanding the why. Different things motivate different people and they’re all very valid. For some, it’s about technology and being on the front edge of technology. For others, what gets them up for work in the morning is seeing those aircraft fly. Many of us are veterans—our sons and daughters are in the military—and that’s a motivator.