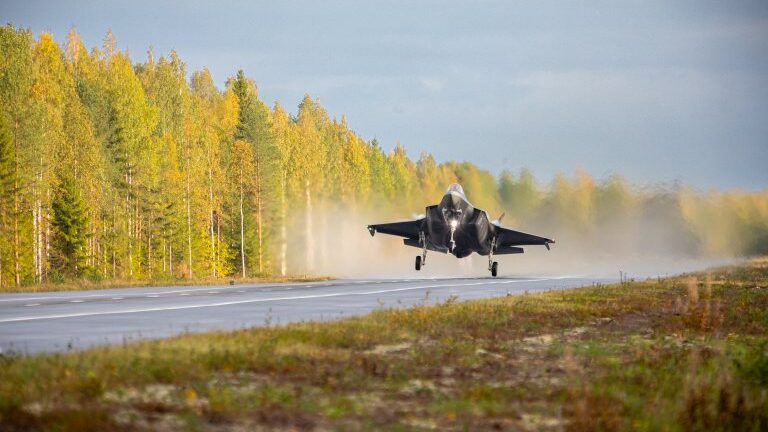
A Royal Norwegian Air Force F-35A fighter jet takes off from a highway in Finland for the first time (Norwegian Armed Forces)
WASHINGTON — As F-35 program officials ponder whether to launch a new competition to replace the stealth fighter’s incumbent cooling system, Honeywell Aerospace today unveiled its own offering for turning down the temperature on the Joint Strike Fighter.
It’s a solution that a company executive said in an exclusive interview would largely retain the jet’s current cooling architecture, should positive tests with a digital twin translate as well as the company hopes to the real world.
For several years, according to previous watchdog reports, a cooling problem has been brewing for the F-35. Although a notable upgrade to the jet’s engine is expected to head off near-term concerns, upgrades planned decades down the line threaten to crank the heat higher, prompting officials to seek improvements to the F-35’s cooling apparatus known as the Power and Thermal Management System (PTMS).
Following a request for information from the F-35 Joint Program Office (JPO) that outlined specific cooling targets, Honeywell now thinks it has a solution in sight, which the company’s Defense and Space President Matt Milas told Breaking Defense will require “moving some of the guts” around but largely keep the current PTMS’s “footprint” — obviating the need for more invasive changes to the aircraft.
“From our perspective, we never stopped working on the development and the improvement of the PTMS,” Milas told Breaking Defense.
The potential for better cooling with fewer changes could come into play as the Pentagon weighs replacing the current PTMS, which is made by Honeywell. One competitor has already lined up to vie for the chance should a new competition come to pass: Collins Aerospace recently unveiling capabilities for its own solution known as the Enhanced Power and Cooling System.
RELATED: As the heat rises with F-35 upgrades, inside Collin’s bet on a new cooling system
Honeywell’s new cooling system doesn’t have a name of its own — perhaps owing to the proposition that it’s a less invasive solution — but Milas said it did recently hit a key benchmark outlined by the JPO: a capacity for 80 kilowatts of cooling. Basically, that means that if the aircraft’s subsystems generate 80 kilowatts of heat, the PTMS has the capacity to sufficiently cool them off.
“Now that we understand that 80 kilowatts is a must-have, it was the mission of: how do we get there, with the lowest impact to the overall airframe?” he said.
How It Works
According to Milas, Honeywell’s solution works by upgrading the jet’s heat exchangers to boost their cooling capabilities, as well as improving the flow of liquid coolant. The company’s approach also plans to leverage other heat sinks on the aircraft to help provide additional cooling.
“The key thing on the heat exchanger design and being able to get more of that thermodynamics out of them is we’re actually building it into the footprint of the PTMS and moving some of the guts of it around to make room. So that’s a key feature that reduces the potential impact of a retrofit capability for things that are out in the fleet,” Milas said.
Honeywell’s solution was demonstrated using a digital twin of the PTMS, leveraging data gleaned from the company’s Torrance, Calif., PTMS test facility and flight hours from the system itself. By modeling it digitally, Milas said the demonstration showed key features, like how the fix would integrate with the jet and interact with other subsystems.
“Through those digital tools, and that digital model, we can simulate what it’s going to actually do on the aircraft, and what the impacts are going to be for the aircraft,” he said.
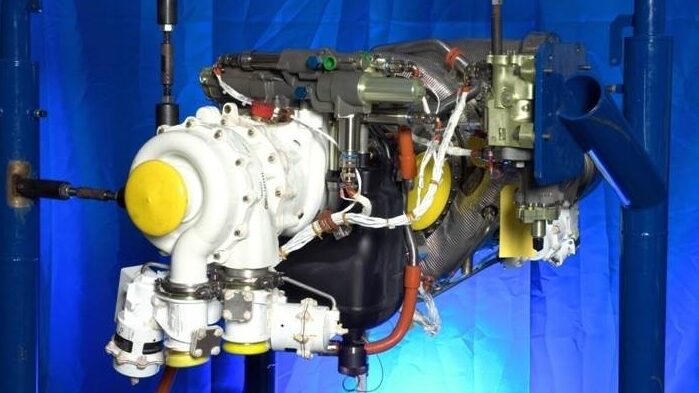
The Power and Thermal Management System (PTMS) made by Honeywell Aerospace. (courtesy photo from Honeywell Aerospace)
That’s critical, Milas said, because the PTMS does more than just cooling. It’s responsible for other crucial tasks like emergency electrical power, with Milas likening it to the aircraft’s “circulatory system” akin to the one that exists in the human body. The digital twin, the company hopes, will closely represent how the fix would work in the real world.
Asked how he’s sure that Honeywell’s model has high enough fidelity to be trusted, Milas said that the current PTMS test facility is what’s used for production and that the model is “proven in reality” as a result. He cautioned that the model for the new PTMS solution is not “complete[ly] finished” — more work will be needed during detailed design efforts to nail down specifics — but he was confident that its results are reliable.
“From a representative technology model of what we can do, this model is as close to production as you can get,” he said.
Milas said the reworked PTMS also will not require more of what’s known as bleed air from the fighter’s engine and consists of “pretty straightforward” upgrades that he said have all achieved the Pentagon’s Technology Readiness Level 7 or higher. The solution further incorporates “other changes that happen across the airframe,” Milas said, though those are “well understood and modeled into the system.”
One point previously raised by Milas is the potential need to widen the tubes that carry coolant liquid — which would be a more invasive change that would require steps like new drilling. Milas said Honeywell’s judgment is that the company’s solution wouldn’t “need to make a big impact on increasing diameter for large parts of the liquid loops,” though “I wouldn’t say that we’re at a point where we can totally rule that out.”
Milas emphasized keeping as much of the current PTMS architecture in place as possible can help keep costs down and minimize development risks along with other possible disruptions, such as the need to find new suppliers for components as the solution is retrofitted on existing aircraft and cut into production.
Although Milas pointed to the efficacy of the digital twin, he said he still expects challenges to arise in how the company’s cooling fix interacts with other subsystems across the aircraft.
“Probably the biggest challenges are going to be, as you design in the changes to the system, any potential impacts to other systems,” he said. “We’re very comfortable and know the PTMS, but anytime you’re changing stuff in the overall architecture, it can have other ancillary effects.”
The company is working with Lockheed to model what some of those potential impacts might be, he said, though putting something new in is “always the big unknown.”
The Competition Question
Honeywell’s offering comes as a question looms over the program: whether a competition for a new PTMS will take place at all.
In a December hearing on Capitol Hill, F-35 program head Air Force Lt. Gen. Mike Schmidt indicated he was leaning toward wider industry involvement, possibly indicating a competition could be in the works.
“There are a number of great suppliers of power and thermal management systems out there that I want to be in this discussion and will be in this discussion. But I’ve got to do some really good engineering work first to try to bring all of that together,” the general told lawmakers.
The prospect of a face-off has been a particularly thorny issue for Honeywell, which has suggested impropriety on the part of F-35 engine-maker Pratt & Whitney and Collins, fellow subsidiaries of RTX. The engine and PTMS work together to help cool the fighter off, and officials have said designing both the engine and PTMS upgrades in tandem will help optimize their respective designs. (In Breaking Defense’s previous report, Collins officials said that company and Pratt had erected firewalls between them when it came to PTMS development.)
Honeywell has previously expressed interest in gaining more technical information on Pratt’s upcoming powerplant enhancement, known as the Engine Core Upgrade (ECU). Milas told Breaking Defense that’s still the company’s goal “so we can best take advantage of whatever those upgrade’s capabilities are.”
Milas also pointed to the decision to sole-source the ECU to Pratt, reasoning that much of the same logic applies to upgrading Honeywell’s PTMS.
“I look at that very similar[ly] when I think about who has the experience and the skills and proprietary technical documentation, the software algorithms and the technical expertise required to furnish the PTMS upgrade,” Milas said of the ECU. “So I would hope that [the JPO] would come to the same conclusion as they did on the ECU, that this is the right thing to do for the program to reduce the technical risk and to minimize the cost and potential impacts to the overall program.”
Backlog of upgraded F-35s could take a year to clear: GAO
“I’m not looking in any way, shape, or form to re-litigate how we got here, where to place blame. I don’t care. At this point, I don’t care,” said Rep. Rob Wittman.